Latest News
-
Scientist warns that hurricane risk to Gulf Coast is increasing 20 years after Katrina
A new study warns that the Gulf Coast of America is becoming increasingly vulnerable to hurricanes. This comes 20 years after Katrina destroyed New Orleans and hundreds of kilometers of coastline. Marc Bove is a German Reinsurer Munich Re meteorologist who warned that with time, the likelihood of major hurricanes making landfall in the area will increase and the effectiveness post-Katrina of flood defense systems would diminish. Katrina, the worst hurricane to ever hit the United States, made its debut in August 2005. It began in Florida, then intensified when it reached the Gulf of Mexico. The storm caused nearly 1,400 fatalities and a total of $205 billion, inflation-adjusted, in damage. "The hurricane risk is increasing, and it's not just in the Gulf area." Bove told. Bove stated that today's Katrina would cost more, and not just due to inflation. The flood protections in New Orleans will gradually erode due to rising sea levels and sinking ground levels. (Reporting and writing by Alexander Huebner, editing by Rachel More).
-
Gold falls with Fed Chair Powell's Speech on Radar
Gold prices fell on Friday, as the U.S. Dollar strengthened. Investors were also awaiting Federal Reserve Chair Jerome Powell to speak at the Jackson Hole Symposium for clues about the central bank's policy. Spot gold fell 0.5% to $3,322.43 an ounce at 8:43 am EDT (1243 GMT) while U.S. Gold Futures fell 0.5% to $3,364.20. Investors backed off rate-cut bets in anticipation of Powell's address at 10:00 a.m. ET (1400 GMT). Powell's speech at the annual Jackson Hole Economic Conference comes amid unprecedented pressure from President Donald Trump on the central banks. However, mixed economic data could pull Powell towards a middle-ground that leaves many major questions unresolved. David Meger is director of metals and futures trading at High Ridge Futures. Any signals about possible rate cuts this year may have a significant impact on gold prices. Even subtle hints will have an impact. "I believe we will see (Powell), take a more cautious stance, considering that two important pieces of economic information, the PCE report and the jobs report, still need to be submitted before the September meeting." CME's FedWatch showed that traders now see a 71.5% probability of a rate cut of 25 basis points in September. This is down from 85.4% one week ago. Gold is usually more profitable in low-interest rate environments, since it offers no yield and looks more attractive compared to other assets that pay interest. In other parts of Asia, gold demand was subdued as price volatility held buyers back. However, jewellers have resumed their purchases in India ahead of the festival season. Silver spot fell 1% to $37.78 an ounce. Platinum fell 1.1% to 1,338.25 and palladium dropped 0.5% to 1115.77. Ashitha Shivaprasad, Bengaluru (Reporting and Editing by Jan Harvey).
-
Aldebaran, a Canadian company, plans to invest $1.5 billion in Argentina's copper project
Javier Robeto, the country manager of Aldebaran Resources Canada, said that at least $1.5 billion will be needed to develop the Altar copper project located in northern Argentina. Robeto stated that the company will include this figure in its preliminary assessment of September. This will show Altar has about 32 billion pounds copper resources and approximately 6.7 million ounces gold resources. Aldebaran does not know if it will be able to spend the money in time to qualify under RIGI (the government's incentive program), which provides long-term tax breaks as well as access to international dispute tribunals for investments above $200 million. The scheme will continue to accept applications until July 2026. There is a possibility of an additional year. It's not sure we'll make the cut. What happens if RIGI is stopped? Robeto explained that the tax burden would automatically return to 54%. RIGI has approved only two lithium mining projects so far, both of which were implemented in October by President Javier Milei. Glencore and McEwen Mining, among others who are working on copper projects, have also applied for the program. Robeto has not provided a timeline for the construction and production of Altar. The estimated lifespan is 20-25 years. The economic assessment includes two scenarios of copper production in either cathode or concentrate form. Robeto explained that the idea was to do a trade-off, examining both pros and cons. (Reporting and Writing by Lucila SIGAL, Editing by Jan Harvey).
-
Rainforest to retail - Indonesian women protecting nature through work
Women use flowers and plants for ecoprinting Sustainable livelihoods protect at-risk rainforest Families can get help with food and school fees by receiving income By Leo Galuh A group of women who work in a conservation park located in Citalahab Sentral - a small village inside Gunung Halimun-Salak National Park - aims to show that nature protection and earning a living can be compatible. Ambu Halimun (which means "Mothers Of Halimun" is Sundanese) gathers foliage rich in natural colours and tannins. Ecoprinting is a technique that uses the flowers and leaves to transfer pigments onto the fabric. Ambu Halimun sells the skirts, scarves, and tote bag made from the intricately-printed fabric in international markets. The women have carved out a livelihood that is sustainable from the rainforest, without having to cut down trees or hunt wildlife. The group is still a small force, but it is growing. It is aiming to become a powerful enough force to make a difference in protecting Indonesia's natural environment. According to United Nations statistics, Indonesia is a biodiversity hotspot. It has a large share of the global flora, fauna and flowering plants, including 17% of bird species. Orangutans and Javan gibbons, Sumatran Tigers and Sumatran tigers are just a few of the critically endangered species that live in its rainforests. Deforestation caused by mining, agriculture and infrastructure is a serious threat to biodiversity. Global Forest Watch reports that between 2002 and 2024 the country lost 10.7 millions hectares (26,4 million acres) in humid primary forest. The human population is growing but the land is limited. They will now be the ones to lead the conservation effort because they have the knowledge and skills to do so," says Rahayu Oktaviani. She is the co-founder of the Javan Gibbon Conservation group, Konservasi Ekosistem Alam Nusantara. JAVAN GIBBONS Citalahab Sentral, with fewer than 300 inhabitants, relies on small-scale farming and tea farming. Tourism through homestays, forest treks, and other activities is also available but it provides inconsistent income. The KIARA group started offering training to residents in ecoprinting and sewing, natural fertilizer production, English, and public speaking after the pandemic devastated local tourism. Tourism earnings are still far below the pre-pandemic level, despite a slow return of guests since 2022. Yuliana is a mother of 4 and a member of Ambu. She said that the income she received from her husband's homestay was not enough to cover daily expenses. She now prints fabrics with motifs of the flora. Yuliana (who goes by one name) said, "I had no idea that leaves would produce natural colors to make ecoprint." KIARA, together with the women, has identified at least 24 rainforest plants species that contain tannins - natural compounds which bind colors to fabrics and prolong their life. Members of Ambu Halimun sell their products through social media, as well as to tourists. They accept orders via Instagram, and prices range from 250,000 Rupiah ($15) up to 700,000. The group's ecoprint signature is a Javan Gibbon motif. Sharing stories about the gibbon habitat and the threats that it faces due to deforestation, hunting and other factors helps raise awareness of conservation in the local community. The gibbon, a small ape that has silver-grey hair and a black facial pattern, is in danger. According to the International Union for Conservation of Nature (IUCN), there are only 4,000-4500 gibbons left in Indonesia. FOOD AND SCHOOL FEE Ambu Halimun's Wulan says her ecoprint earnings have made a real difference. She said that the majority of her family's expenditure is on food and school fees for her children. If he works for 20 days, her husband, who is a tea picker earns between 800,000.00 ($49) to 1,140.000 ($70). Many families borrow money in order to survive, and end up in debt. Ecoprint pays me 2 million Rupiah (122 dollars) every quarter. "It's enabled me to save," Wulan said as she removed the boiled marigold flower from the fabric. KIARA plans to expand its ecoprinting efforts, but its artisanal character means that its size will be restricted. Harumi Supit is vice president of Amartha Financial's public relations department. Amartha Financial provides services to more than 3.3 million women owned businesses in rural Indonesia. She said that to reach and sell in bigger markets, they require resources, transport and channels of distribution as well as careful planing. She said that maintaining quality standards is a challenge when you want to reach a wider audience. Ambu Halimun sold 41 pieces in 2020, and 237 the previous year. By mid-2025 it had reached 130 sales. Oktaviani said that KIARA’s role is to expand the group, encourage residents – especially women – to adapt to the post-pandemic changes in the economy and to find solutions within the environment. She said that they have an in-depth knowledge of the native plants. She said that the leaves used in ecoprint were often the same ones used traditionally for herbal remedies or as raw food. It's rooted into traditional knowledge which is slowly disappearing. She said that the project is not only helping to keep the forest intact but also empowers women, who "used to be tucked in the kitchen."
-
Stocks on hold as traders wait for Powell's speech
The stock market was largely flat on Friday, as traders awaited the key speech by Federal Reserve Chairman Jerome Powell this weekend at the annual Jackson Hole Symposium that could shed some light on future monetary policy. Powell's previous speeches at this event have often moved the markets. This year's remarks will be closely scrutinized as his position is under heavy scrutiny from U.S. president Donald Trump. There are concerns that the Fed's autonomy could be threatened. Investors have reduced their bets that the Fed will cut rates at its September meeting due to a surge in U.S. Producer prices. This is down from 85% a week earlier. The Jackson Hole event also featured other Fed speakers who were lukewarm about the idea of a cut in September, despite recent signs that the U.S. labor market is weakening. Nabil Milali said that a cautious tone from Powell regarding the prospects of a September rate cut, deferring to future jobs and inflation data, could be enough to reduce market pricing down to a 50/50 call. Milali said that Powell could also decide to defend the Fed’s independence. He said that he believed the unofficial topic of this meeting was central banks' autonomy. MSCI's broadest global stock index was essentially flat for the day after European stocks rose in the morning before the speech. Wall Street futures are up between 0.1-0.2%. China's CSI 300 Index rose 2.1% after DeepSeek upgraded its flagship V3 AI Model and reported that Nvidia asked Foxconn suspend work on the H20 AI Chip, lending support for Chinese rivals. The dollar index (which measures the greenback versus six peers) edged up 0.1%, while the euro fell 0.1% to $1.15985, after an official revision showed that Germany's second-quarter economy contracted by 0.3%. Data from Japan showed that core consumer prices fell for the second consecutive month in July, but they remained above the central banks' 2% target. This has kept alive expectations of a rate increase in the near future. This did not help the yen much, as it was on track for a 1% drop for the week. BOJ Governor Kazuo Ueda is also scheduled to speak in Jackson Hole, Wyoming this weekend. Brent crude oil prices fell, Brent crude trading at $67.5 a barrel last, down 0.2% from Thursday's gains as Russia and Ukraine blamed one another for the stalled peace processes. Gold spot fell 0.2% to $3,330.9 an ounce.
-
Copper prices rise on strong demand in advance of Powell's speech
The copper price rose for the third time in a row as China, the world's largest metals consumer, remained strong and investors hoped that a speech from U.S. Central Bank chief John Williams would indicate interest rate reductions. The benchmark three-month copper price on the London Metal Exchange rose 0.2% to $9,745 per metric ton. This is down from a high of $10,020.50 reached on July 2. It was its highest in more than three months. The Chinese demand for the metal remains healthy, according to Nitesh Sha, a commodity strategist with WisdomTree. Last month, U.S. president Donald Trump imposed tariffs of 50% on copper products. However, he excluded ores, concentrates, and cathodes. The Yangshan Copper Premium is a premium in China Since August 11,, which represents the demand for imported copper into China, is up 13% at $51 per ton. Investors await the speech of U.S. Federal Reserve chair Jerome Powell at the annual Jackson Hole Conference in Wyoming, due to start at 1400 GMT. Shah said that if there is any indication of a dovish tilt, it could be a very positive for copper prices because that would keep demand up. The dollar index was firmer on Friday, after some Fed officials were hesitant to cut rates next month. The dollar is stronger, and therefore the prices of commodities in U.S. dollars are higher for foreign buyers. LME aluminum also increased, adding 0.15%, to $2,589 per ton. Analysts at Guosen Futures on Friday said that the anticipation of a seasonal increase in demand next month could have helped to boost aluminium prices. Other metals include LME Zinc, which rose 0.8% to $2.787.50 per ton. Lead gained 0.6% at $1.981, Tin increased 0.1% at $33,465, while Nickel fell 0.1% at $14,920. (Reporting and editing by Jan Harvey; Additional reporting in Beijing by Amy Lv; Reporting by Eric Onstad)
-
Dollar firms as gold falls, but Powell's Jackson Hole remarks are in the spotlight
The dollar's strength caused gold to fall on Friday. Markets are awaiting Jerome Powell's address at the annual Jackson Hole Symposium for further insight into the Fed's monetary policies. By 0817 GMT spot gold had fallen 0.4% to $3,326.35, while U.S. Gold Futures for December Delivery were down 0.4% to $3,368.80. UBS analyst Giovanni Staunovo stated that the moderately stronger U.S. dollar was playing a significant role in the current gold pullback. Gold becomes more expensive to overseas buyers when the dollar is stronger. Investors reduced their expectations of a Fed rate reduction in September, causing the dollar index to rise to a two-week high. According to CME's FedWatch, futures markets now indicate that there is a 71% probability of a rate cut by a quarter point next month. This is down from over 90% a week ago. In a low-interest rate environment, non-yielding gold tends to perform well. Fed officials appeared to be lukewarm on the idea of a cut in rates next month, as investors prepared for Powell's Friday 1400 GMT speech. Staunovo stated that their comments indicate the next U.S. Central Bank meeting will be "intense, with some favoring large cuts while others (favor) no movement at all". Fed policymakers face a challenge because, despite signs of a weakening labour market, inflation is still above the central banks' 2% target. It could even go higher as a result of the Trump administrations aggressive tariff increases. Recent data on the US labour market showed that unemployment claims in the United States rose by nearly three months last week, and the week before they reached a four-year high. Silver spot was down 0.4% to $38.03 an ounce. Platinum fell 0.6% to 1,343.80 and palladium increased 0.2% to 1,112.85. (Reporting Ishaan Arora in Bengaluru; Editing by Jan Harvey)
-
China tightens its grip on rare earth supply quotas
China, which is the dominant supplier of rare earths in the world, announced on Friday new measures to regulate mining, smelting, and separation of these critical minerals that are key to the energy transition. This will further tighten its grip on supply. Beijing regulates, manages and controls rare earth mining and smelting via a quota-based system. In a recent statement, the Ministry of Industry and Information Technology announced that these new rules would include imported raw materials within that system. The process of public consultation began in February. Analysts said that the inclusion of imported iron ore indicates a tightening in supply. Companies were concerned that they might lose their access to feedstock. Rare earths is a grouping of 17 elements that are used in products ranging from magnets in wind turbines, electric vehicles and consumer electronics to lasers in military equipment. In April, in response to the U.S. tariff increases, China added several rare earth products and magnets on its export restriction list. The first 2025 mining and smelting license was quietly released Quotes Without making its usual public statements, reported last year, citing sources. Reporting by Beijing Newsroom and Lewis Jackson, Editing by Muralikumar Aantharaman and Kate Mayberry
DOE: America Can Recycle 90% of Wind Turbine Mass
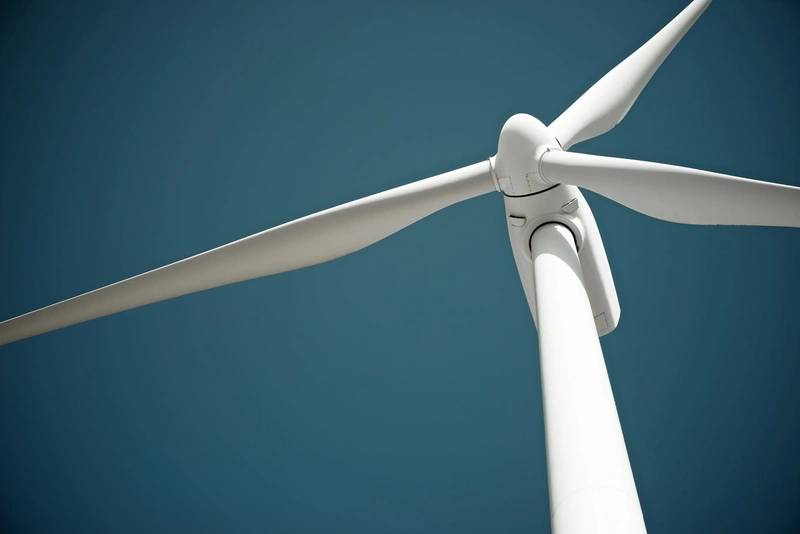
A new report from the U.S. Department of Energy (DOE) outlines recommendations that could increase the recycling and reuse of decommissioned wind energy equipment and materials to create a more circular economy and sustainable supply chain.
The research reveals that existing U.S. infrastructure could process 90% of the mass of decommissioned wind turbines. However, the remaining 10% will need new strategies and innovative recycling methods to achieve a more sustainable wind energy industry.
The Recycling Wind Energy Systems in the United States Part 1: Providing a Baseline for America’s Wind Energy Recycling Infrastructure for Wind Turbines and Systems report will help guide over $20 million in investments previously announced from the Bipartisan Infrastructure Law to advance technologies that address this gap.
The effective reuse and recycling of wind system components, parts, and materials will rely on a combination of measures, including:
• Improved end-of-life decommissioning collection and scrap sorting practices.
• Strategic siting of recycling facilities.
• Expanded and improved recovery and recycling infrastructure.
• Substitution of hard-to-recycle and critical materials with more easily separable and affordable materials, improved component designs and manufacturing techniques or the development of modular system components.
• Optimized properties of recovered materials for second-life applications.
• Greater access to wind energy waste streams and the equipment required to disassemble wind energy components.
Towers, foundations, and steel-based subcomponents in drivetrains offer the greatest potential currently to be successfully recycled, whereas blades, generators, and nacelle covers are likely to prove more difficult. Recovering critical materials and alloying elements from generators and power electronics, such as nickel, cobalt, and zinc, will be crucial in establishing a circular economy for wind systems.
Short-term strategies for decommissioning include promoting blade production using more easily recyclable thermoplastic resins and reusing these resins in cement production. Thermoplastic-based blade recycling technologies, such as pyrolysis and chemical dissolution, could be viable medium- and long-term options. Other medium- and long-term solutions include high-yield techniques for separating compounds found in power electronics and hybrid methods for recycling permanent magnets.
Regional factors - such as material demand, disposal fees, transportation distances, and an available skilled workforce - will play vital roles in ensuring the success and cost-competitiveness of recycling wind energy components.
A team of researchers, led by the National Renewable Energy Laboratory with support from Oak Ridge National Laboratory and Sandia National Laboratories, prepared the report. The first of a suite of reports, this part provides DOE’s Wind Energy Technologies Office with short-, medium-, and long-term RD&D priorities along the life cycle of wind energy systems.
“The U.S. already has the ability to recycle most wind turbine materials, so achieving a fully sustainable domestic wind energy industry is well within reach,” said Jeff Marootian, principal deputy assistant secretary for the Office of Energy Efficiency and Renewable Energy. “Innovation is key to closing the loop, and this research will help guide national investments and strategies aimed at advancing technologies that can solve the remaining challenges and provide more affordable, equitable and accessible clean energy options to the American people.”
DOE recently announced an investment of $20 million to improve the recycling of wind energy technologies, and in September 2024, DOE announced six final winners of the Wind Turbine Materials Recycling Prize. This $3.6 million competition expands domestic capabilities for the recycling and recovery of wind materials as teams use their winnings to bring their technologies closer to commercialization.